Water security, taking the plunge into permaculture earthworks.
Posted on February 19, 2018 by WormBiz
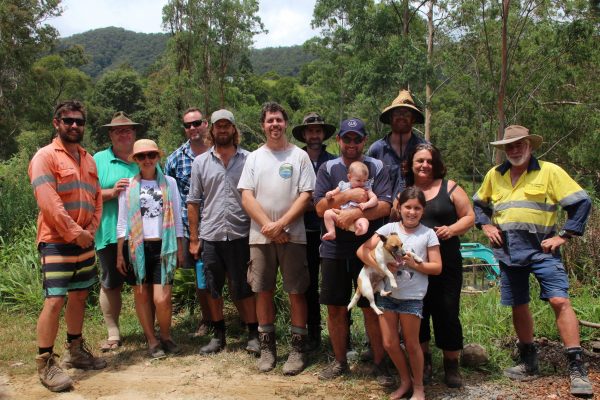
Permaculture earthworks – an open consultancy with Zach Weiss (Protégé of Sepp Holzer)
Our vision
It isn’t very often that a farm undergoes a complete overhaul and it’s one that can be daunting. So this time we chose not to do it alone. Here’s a closer look into working with a professional consultant, from the design phase through to implementation, and the joy of sharing the experience with 10 enthusiastic people.
This next stage in our “farm journey” has proved to the biggest and most ambitious and one that, most importantly, would build resiliency into our farm business and also into our lives. We jumped at the opportunity to have Zach Weiss help us tackle the big decisions we faced.
Zach is from Elemental Ecosystems and trained with ecology specialist Sepp Holzer. He’s the first person to earn the Holzer Practitioner certification directly from Sepp after completing a rigorous two-year apprenticeship working on projects in Europe and North America. The excellence of work performed by Sepp and Zach speaks volumes of what’s possible in creating water-retentive landscapes. Our group was captivated by the expertise of Zach’s presentations and the insight into the array of projects he and Sepp have undertaken worldwide.
Our farm’s transformation revolved solely around water – its flow, capture, storage and use. Starting with the site’s analysis, we were able to initiate elements of design, form a working plan, then organise and move into the implementation – major earthworks! The most important component was keeping an open dialogue with Zach.
Key points for site analysis
Slope, vegetation (including large trees), land formation and gradient, solar aspect, water flow, material/soil types and property boundaries.
Earthworks can be very expensive and putting our ambitious, yet achievable, plan into action proved to be the most difficult part. Problems can happen along the way and these significantly affect what you can physically get done and, of course, the final cost. I learnt many valuable lessons and realised that my previous communications with contractors have been absolutely to my disadvantage when the job was done incorrectly and hugely more expensive than I would have liked.
Test slices
The real learning curve for me, and the participants, was the limitation on the design without the right information. It didn’t matter about the previous proposals or plans we had in mind because until we knew what was beneath the surface, we didn’t know what strategies were needed. It is now clear – from here on I need to design around what is in the ground not how the land formation seems.
Not only did we have 10 participants here itching to get into the project, we had a 23 tonne excavator on site too. Problems remember? Our first arose at the start – the digger got stuck in the driveway when one of its tracks dislodged during unloading from the float. Our access was blocked for the next 12 hours while the machine was repaired; and this proved to be the first good lesson in how to deal with things going wrong. As part of the open consultancy, participants were able to work through the issues and saw many decisions being made that were not part of the plan. The machine was a big tired old girl and considering the amount and type of work we were attempting, a slipped track this early in the game was a concern. Nonetheless, we continued on and this minor speed bump made one thing clear – check when hiring equipment – its age, reliability and condition.
Expertise matters
It is essential to have the knowledge and experience on hand if and when difficulties arise. Our plans were changed as we went along and that was the beauty about working with a seasoned professional – it gave us the ability and flexibility to process problems effectively. Zach was great and always prepared to get dirty when the dirty needed to be done! Experience is a major factor and knowing how to adapt to make good decisions quickly is essential to ensure the work is performed correctly. We all hear that sometimes contractors will take short-cuts to suit their own purposes, but ultimately you are the one that wears the cost. So this is when a consultant pays dividends.
Day one
A farm tour and site analysis was done first thing on Saturday morning and the group could see the reasons why test slices are so critical to a successful dam project. The earth samples allowed us to determine three possible sites – but all had advantages and disadvantages.
The first possibility looked a good dam site but this waned as the amount of desirable clay material diminished with every bucketful we extracted. The second site produced a good slice as we found some pretty good clay deposits but the size of the dam wall and the lack of moisture deep-down was problematic, so we moved straight onto the next. The third slice, which ended up being our main pond feature, seemed to have some really good clay and the moisture levels were perfect as water seemed to be moving through the sub-surface. The only problem with this site, and why it was not our initial preference, was the constraints with property boundaries and natural water flow.
Day two
The second day started with a minor diesel spill before the bacon even started sizzling! Our acreage is steep and our visiting group parked cars and pitched tents nicely where space was at the ready. But the excavation contractor was short of space and parked the truck in an unusual position which resulted in fuel, from the refuelling tank, to pour out from a loose flange. We sprang into action with the excavator’s operator but it was some time before we were able to resolve the problem. Litres of diesel spewed onto my driveway. We have kept our place chemical free and this was the first time something like this has happened. It was hard to take and extremely disappointing – I did my best to capture it which resulted in keeping the discharge contained. Another valuable lesson – when working with contractors on your property careful consideration to equipment placement is paramount – check everything twice.
It wasn’t long before the machines were getting stuck into it. We had the big machine move some fallen trees and rework the bottom terrace that wasn’t built properly, so we had to entirely change the level for the water to actually run the right way. While the big machine was in action, the smaller three-tonner was removing top soil and making some room for the big girl to move-in later. The restriction with these two terraces was a couple of large trees that we were hoping to keep as privacy from neighbours and the tightness between the existing terraces.
“The expense of earthworks, especially when unforeseen circumstances come into play, like breakdowns, inclement weather and the wrong material types, can be quite overwhelming if you get half way through the budget and you’ve completed less than half the work.”
Terrace design
We run a commercial worm farm so knew that controlling leachate was going to be a big part of the design due to the high annual rain fall; around two metres. So designing a three pond system to deal with the large volumes of water and to remediate the nutrient was our best bet. As part of the project, we wanted to primarily control nutrients, treat the water and then reuse it in the existing worm production area. We also envisaged watering gardens and establishing potential vegie production plots. The first thing to get right on the terraces was the water flow and making them lean into the gully leachate ponds. Step two – they needed to be big enough for the worm habitat and allow vehicle manoeuvrability; to grow and service the worms using my small 23 horsepower tractor. And lastly, I wanted to build rigid overhead structures for shade and watering while having the ability to plant trees/shrubs/vines to utilise its framework.
Terraces work
Terrace systems are beneficial in many ways and the more I work with them the more I’m learning about their true capabilities and value. Slowing water flow, holding water, steering water, flat areas for fast production and batters for trees and vines, are key elements. There is vertical potential too with the ease of building overhead shade structures, microclimates are prominent, accessibility is easy and the views are great. Terraces are special and once they are built correctly they will always produce well.
The water moving through the ground is cleaned and filtered by the whole ecology; it will be crystal clear and mineral rich, and the ponds soon will be abundant with life. Build it they will come! This is an elemental ecosystem and my family’s lives will become part of it; growing memories to share in the future.
The weekend was a real hoot and thanks to everyone that came along. A special thanks to Zach for coming all the way from Montana in the beautiful northwest of America. And most of all, thank you to my wife and family who opened their lives for all to see.
Stay tuned – there’s more to come.
I hope you can join us for the next one.
Follow us at Wormbiz.com.au
Thank you
Peter Axisa